Acetaldehyde, also known as Ethanal, is a colorless liquid with an irritating odor. Melting point – 121℃, , boiling point 20.8℃, relative density 0.7834 (18/4℃), relative molecular mass 44.05. Molecular structure is methyl C atom bonded by SP3 hybrid orbital, aldehyde C atom bonded by SP2 hybrid orbital, molecule as polar molecule. It is soluble in water, ethanol, ether, chloroform, acetone and benzene. It is flammable and volatile. Vapor and air can form explosive mixture, explosive limit 4.0% ~ 57.0% (volume). Acetic acid is readily oxidized.
In the presence of a small amount of acid it is very easy to aggregate into paraldehyde (liquid, melting point 124℃), it generates polyacetaldehyde in low temperature. The two polymers can be decomposed into acetaldehyde by a small amount of sulfuric acid. In industry it is mainly produced by the oxidation of ethanol.
Main applications: used for manufacturing acetic acid, acetic anhydride, pyridine, synthetic resin, rubber, plastic, spices, also used in leather, pharmaceutical, papermaking, medicine, as preservatives, antidotes, imaging agents, solvents, reducing agents, etc.
Main reaction
CH3CH2OH+1/2O2→CH3CHO+H2O -173.1kJ/mol
CH3CH2OH→CH3CHO+H2 +68.9 kJ/mol
Side reaction
CH3CH2OH+3O2 →2CO2+3H2O
CH3CHO →CH4+CO
CH3CH2OH+O2 →CH3COOH+H2O
CH3CH2OH+CH3COOH →CH3COOCH2CH3+H2O
The high-temperature gas at the outlet of the oxidizer is cooled and condensed before entering the absorption column, where water is added on the top to absorb acetaldehyde and unconverted alcohol. Inert gases such as nitrogen are expelled from the top of the column. The dilute acetaldehyde (including acetaldehyde, alcohol, formic acid and water) at the bottom of the column is absorbed and sent to the distillation column for pressurized rectification after heating. Qualified acetaldehyde is obtained after condensation of the gas phase at the top of the column.
The alcohol-water mixture discharged from the bottom of the distillation column is automatically pressed into the alcohol recovery column. The diluted alcohol recovered from the top of the alcohol recovery column is returned to the mixing tank to continue to participate in the reaction, and waste water is discharged from the bottom of the column. The whole cycle is equipped with refrigerator, nitrogen making machine and circulating cooling water device.
Acetaldehyde process flow chart
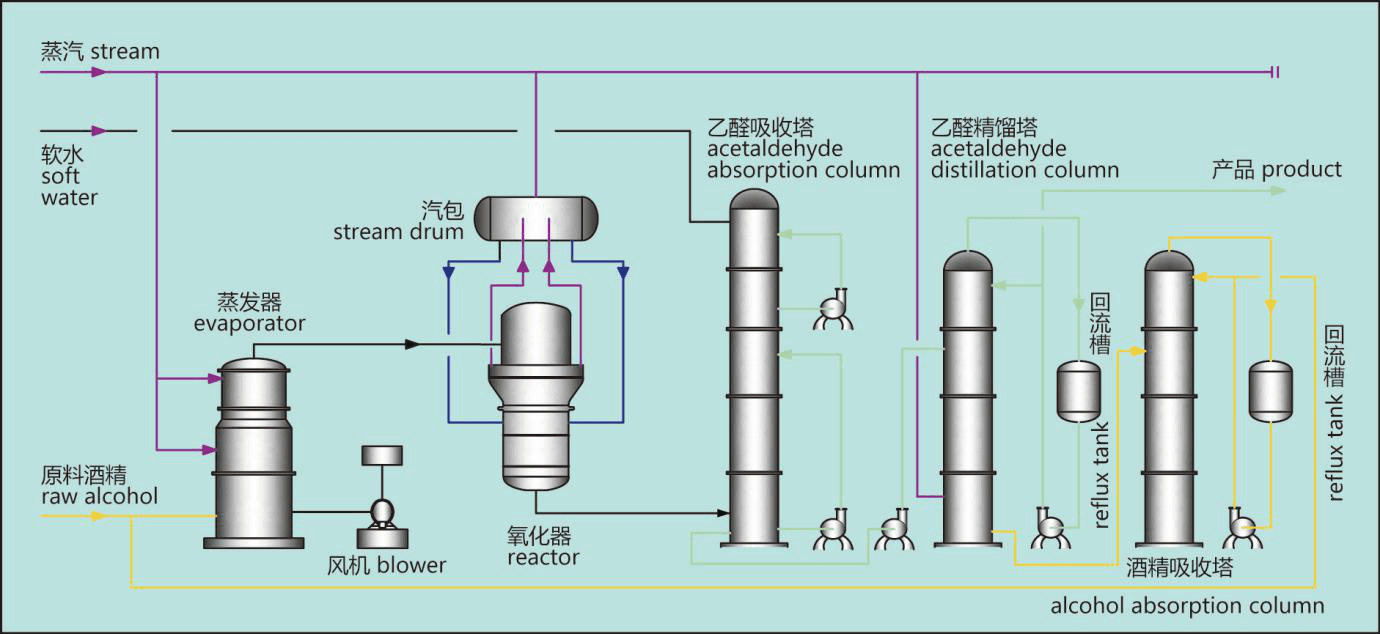
Main raw material consumption
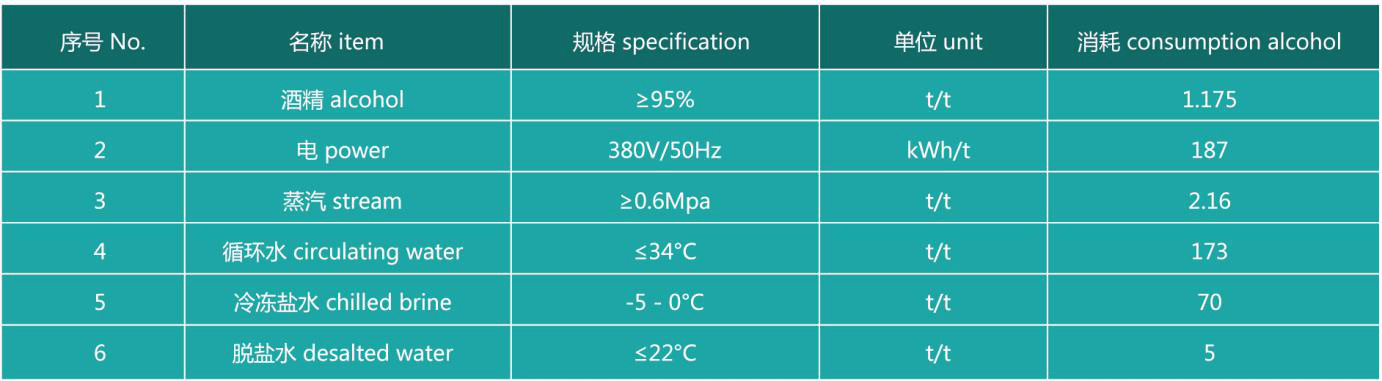
Product Quality

Other process indexes
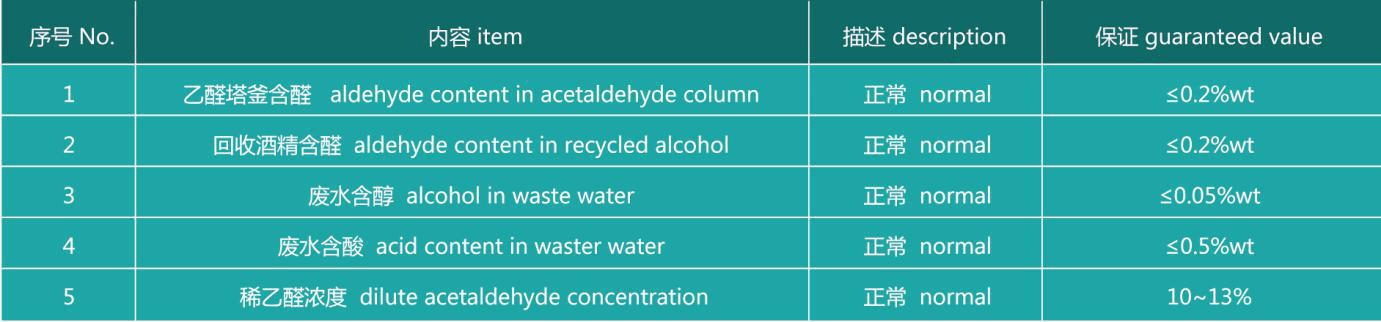
- About Dolton & Helipont
- Formaldehyde production technology
- DMMn production technology
- Paraformaldehyde production technology
- Methylal production technology
- Hexamine production technology
- Acetaldehyde production technology
- Pentaerythritol production technology
- Trimethylolpropane production technology
- Neopentyl glycol production technology
- Trimeraldehyde production technology
- 1, 4-cyclohexane dimethanol CHDM production technology
- EPP production technology
- Production technology of concentrated formaldehyde made from dilute formaldehyde