Hexamine is a white crystalline powder, odourless, slightly sweet, with allergic irritation to skin, gravity 1.331 (20℃), flash point 250℃. It is stable in storage in air, but easy to absorb moisture and agglomerate. Hexamine is flammable and the flame is colorless, melting point 263℃. When it is heated above 100℃ at atmospheric pressure, it sublimates a little and decomposes into methylamine. Hexamine is extremely easy to dissolve in water. The concentration of saturated water solution is 46.5% at 25℃.
Hexamine is a weakly alkaline substance with an aqueous solution pH of 8-8.5. However, the solubility of hexamine decreases with the increase of ammonia concentration. Hexamine decomposes with hydrochloric acid, sulfuric acid, acetic acid and salicylic acid to produce formaldehyde, ammonia, carbonic acid and methylamine. The higher the concentration of hydrogen ion in hexamine, the faster the decomposition rate will be.
Production of hexamine
In the production process of hexamine by gas phase, formaldehyde gas generated by methanol conversion is directly injected into the ammonification reactor, and the reaction with ammonia gas in the saturated mother liquor of hexamine produces hexamine. The process is characterized by the latent heat of formaldehyde and the heat of reaction of hexamine. In the vacuum condition, water is evaporated, so a lot of steam can be saved and the product purity is high.
Liquid phase process
6CH2O(liquid)+4NH3(gas)→(CH2)6N4+6H2O -340Kcal/mol
The process is divided into formaldehyde and ammonia condensation reaction, hexamine evaporation, concentration, centrifugation and drying.
Ammonia gas is configured to a certain proportion (ammonia excess 0.8-1.2%) with formaldehyde solution after filtration and enters into the reactor to generate hexamine with 24-27% concentration. Heat in the reaction is removed by circulating cooler to keep the reaction temperature at 60-65℃. The hexamine solution generated is pumped into the film evaporator for concentration to 60-65%. The moisture is condensed by condenser, and the whole process of concentration is under negative pressure operation.
The concentrated solution in the evaporator continues its dehydration and concentration under vacuum. After crystallization particles are formed, it enters the centrifuge to separate the mother liquid. The solid material is sent into the airflow dryer, and hexamine product is finally separated by cyclone separator.
Gas phase process
Equation as follows:
6CH2O(gas)+4NH3(gas)→(CH2)6N4+6H2O – 745kj/molFrom the equation, hexamine is generated by the reaction of 6 molecules of formaldehyde and 4 molecules of ammonia to form 1 molecule of hexamine and 6 molecules of water while releasing heat.
In production process, in order to make the reaction to generate hexamine, at the same time to avoid the adverse event generated and affect the quality of the product and consumption, the reaction temperature will be well controlled and ensure excess ammonia, i.e., there are free ammonia in the reaction solution, which is able to prevent the occurrence of adverse reaction and resist the formation of trimethylamine, which stinks and will affect the purity of the product.
The gas phase hexamine production technology is short in processing route, with few side reaction, the product purity is high. The recovery of excess ammonia can eliminate environmental pollution and reduce consumption. Comprehensive utilization of heat is reasonable, production is continuous with high automation.
1,The oxidized formaldehyde gas at high temperature is directly pumped into the ammoniation reactor. After filtration and measurement, ammonia gas is fed into the ammoniation reactor. The formaldehyde gas and ammonia gas generate hexamine in the mother liquid of the ammoniation with bubbling reaction.
2,Using formaldehyde latent heat and hexamine reaction heat under the condition of vacuum, to control the reaction temperature at 75-80℃ to evaporate moisture.
3,The hexamine generated in the ammonification reactor is put into a liquid sealing tank, and then sent to the receiving tank. The mother liquid returns to the ammonification reactor, and the concentrated liquid enters the centrifuge to separate the liquid.
4,The finished product is prepared after the solid hexamine is fed into the dryer for further dehydration.
5,The excess ammonia is absorbed in the ammonia absorption column along with the evaporated gas in the reactor, and the dilute ammonia solution in the absorption column enters the ammonia desorption column to recover the ammonia and then returns to the ammonification reactor.
Flow chart of hexamine with gas phase process
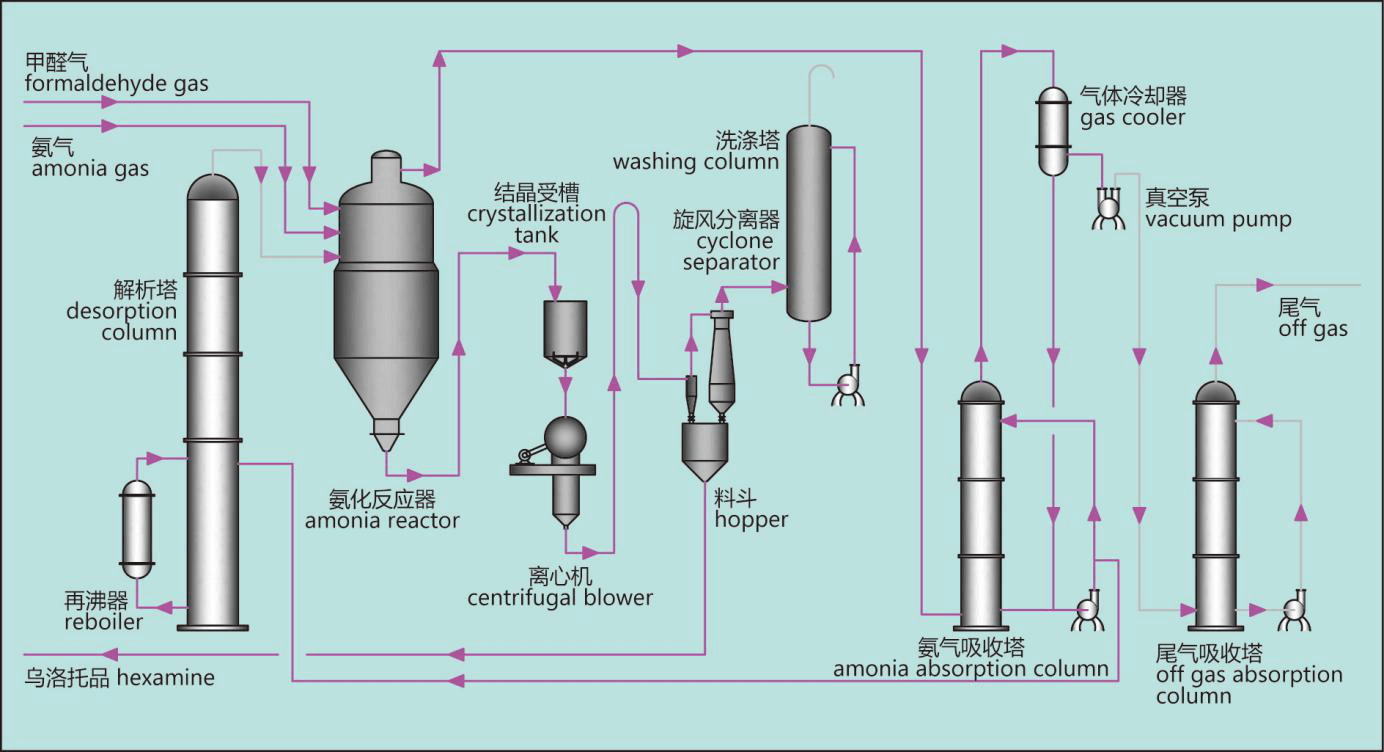
Main raw material consumption
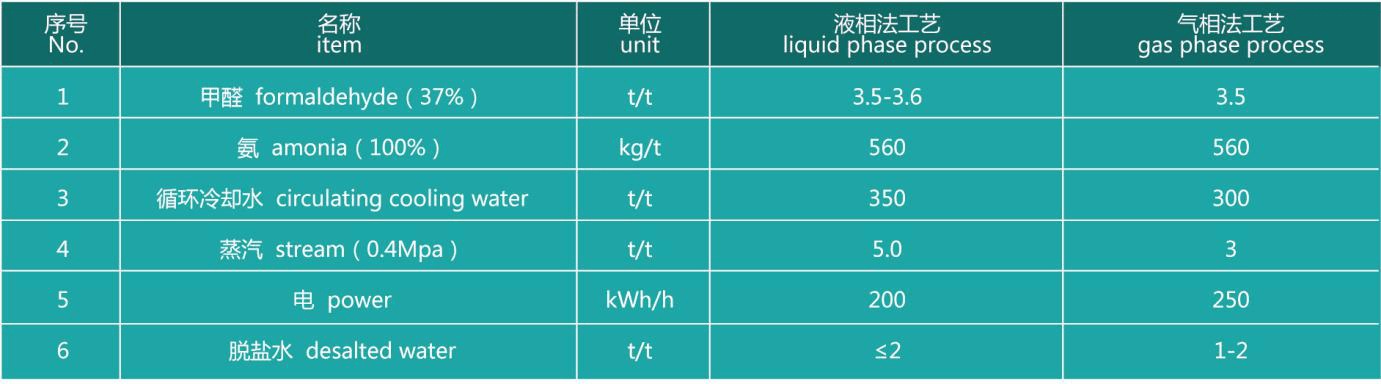
- About Dolton & Helipont
- Formaldehyde production technology
- DMMn production technology
- Paraformaldehyde production technology
- Methylal production technology
- Hexamine production technology
- Acetaldehyde production technology
- Pentaerythritol production technology
- Trimethylolpropane production technology
- Neopentyl glycol production technology
- Trimeraldehyde production technology
- 1, 4-cyclohexane dimethanol CHDM production technology
- EPP production technology
- Production technology of concentrated formaldehyde made from dilute formaldehyde