With years of practice, Dolton has developed a new dilute formaldehyde treatment process. We use methylal as the intermediate to convert the dilute formaldehyde into concentrated formaldehyde between 50% and 69%, and the concentrated formaldehyde goes back as the reaction raw material.
Processes are divided into dilute formaldehyde conversion, methylal oxidation, formaldehyde absorption and off gas treatment
Dilute formaldehyde conversion: after mixing dilute formaldehyde according to certain proportion into the reactor for initial reaction to remove the impurity in the dilute formaldehyde, then feed into methylal reaction column for distillation process, methylal and methanol azeotrope from top of the column is sent to the next unit, waste water discharged from the column will be sent to sewage treatment plant after cooled.
Methylal oxidation: the fresh air is pressurized by the fresh air blower, and the off gas circulating back from the top of the absorption column enters the circulating air blower for pressurization. The methylal produced from the top of the methylal reaction column is vaporized by a methylal carburetor, and the vaporized methylal and the pressurized mixed gas are mixed evenly before entering the reactor. The reactor is provided with a catalyst to promote the oxidation of methylal to formaldehyde. Methylal is oxidized under the action of catalyst to form formaldehyde. C3H8O2+O2=3CH2O+H2O. Compare with the reaction of direct oxidation of methanol to formaldehyde
3CH3OH+1.5O2=3CH2O+3H2O, if the same reaction of 3mol of formaldehyde produced by the formation of water will reduce by 2mol, the formaldehyde concentration obtained by this method is as high as 70%.
Formaldehyde absorption: the high-temperature gas from the reactor first passes through the steam generator and desalted water for heat transfer before entering the absorption column and at the same time by-product of water vapor for exporting. The absorption section is divided into two formaldehyde absorption columns. Qualified formaldehyde products are extracted from the bottom of the absorption column.
Off gas treatment: part of the off gas from the top of the second column will return to the fresh air fan outlet, and the other part will enter the ECS reactor. In off gas, carbon monoxide, dimethyl ether, methanol and so on react with noble metal catalyst to produce carbon dioxide and water, and the by-product steam is sent out.
Process flow chart
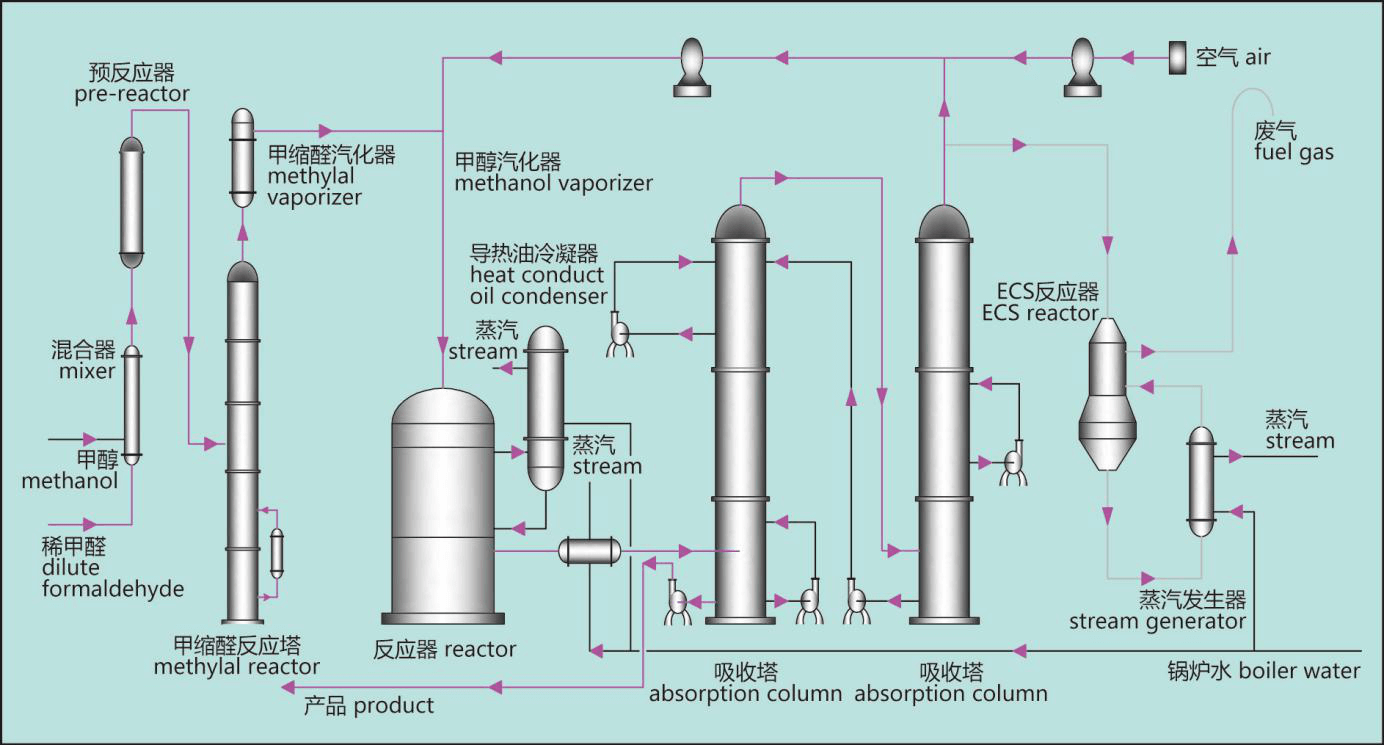
Process comparison
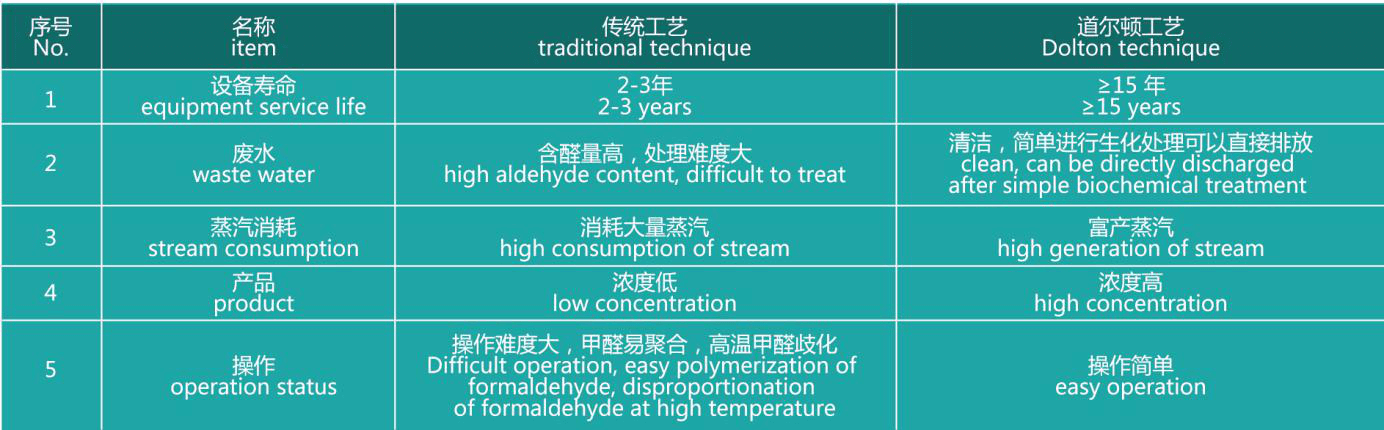
Main raw material consumption
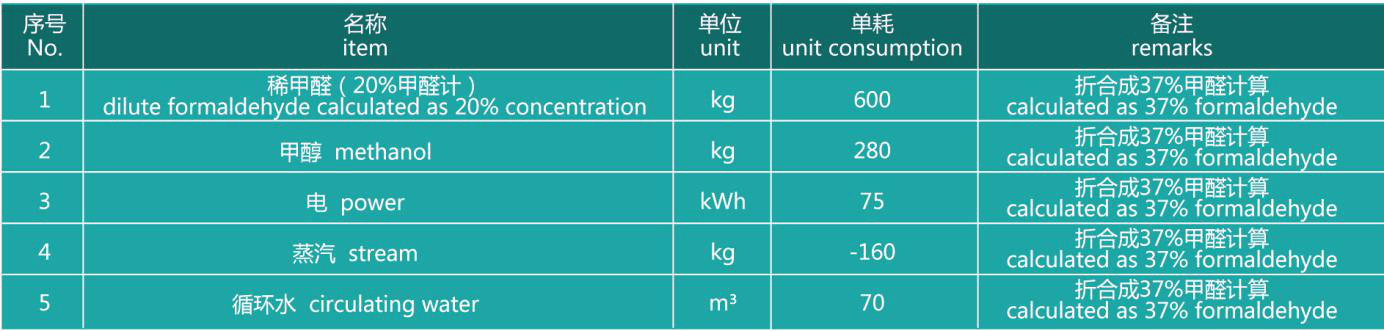
Advantages: short process; Low investment cost
Disadvantages: added value not significant; high consumption of steam and power; difficult to treat wastewater with high ammonia nitrogen content
2,Use dilute formaldehyde to produce methylal.
Advantages: short process; Low investment cost and low steam power consumption
Disadvantages: low added value; Limited market capacity
3,Produce commodity formaldehyde by blending concentrated formaldehyde.
Advantages: low investment
Disadvantages: low added value; limited market capacity; large amounts of high concentration formaldehyde needed
4,Use dilute formaldehydes to produce trimethylolpropane.
Advantages: high added value, big market demand
Disadvantages: long process and high investment
- About Dolton & Helipont
- Formaldehyde production technology
- DMMn production technology
- Paraformaldehyde production technology
- Methylal production technology
- Hexamine production technology
- Acetaldehyde production technology
- Pentaerythritol production technology
- Trimethylolpropane production technology
- Neopentyl glycol production technology
- Trimeraldehyde production technology
- 1, 4-cyclohexane dimethanol CHDM production technology
- EPP production technology
- Production technology of concentrated formaldehyde made from dilute formaldehyde