Trimethylolpropane (TMP) is an important organic chemical intermediate and fine chemical product, which has been widely used in many fields. It is mainly used for the production of alkyd resin and polyurethane, also used in surface active agent, wetting agent, plasticizer, FRP, rosin ester, senior aviation lubricating oil, fiber processing agent, printing ink, the production of polyurethane foam plastic, it also can be used as a resin chain extender, textile auxiliaries, and polyvinyl chloride (PVC) resin thermal stabilizer.
The catalyst used in this method is calcium hydroxide. Because of the presence of trace formats, it can easily lead to the decomposition of TMP during distillation and refining, thus reducing the yield and quality of TMP, the removal of formates is the key to the preparation of high-purity TMP. At present, the main methods of desalting are evaporation, concentration and extraction. The extractive desalting method is divided into single solvent or double solvent method. The conizarro process is the main method for the production of TMP. The process is mature, easy to master and does not require high temperature, high pressure and special catalyst. At present, most TMP manufacturers mainly adopt this method for production.
Conizarro method process flow diagram
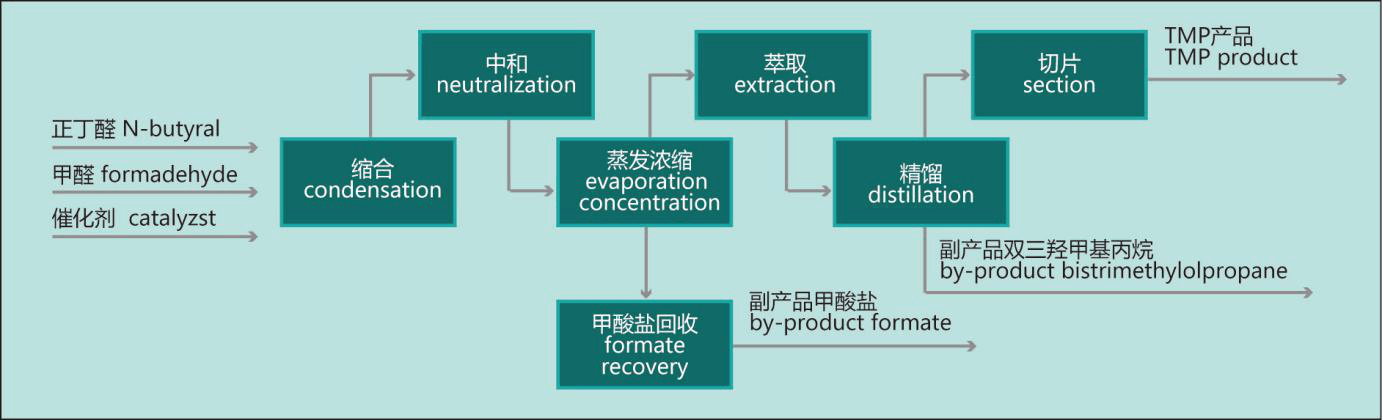
1, In condensation and neutralization process: add quantitative N-butyraldehyde and formaldehyde in reactor with stirrer, in the presence of calcium hydroxide alkaline catalyst, stir up to 40-50℃ for condensation reaction, 2,2-dihydroxymethyl butyraldehyde is obtained during the reaction, then add excessive formaldehyde for Conizarro reaction. After that add formic acid to the reactor for neutralization to reach a certain pH value, that is, the crude reaction liquid containing trimethylolpropane and calcium formate and other by-products of trimethylolpropane.
2, Formaldehyde recovery: the reaction liquid obtained from the above process is sent to the concentration column for concentration, and the unreacted formaldehyde is recovered by double distillation columns. The recovered formaldehyde can be recycled in the previous process, and in this process, a small amount of methanol by-products obtained from the side reaction can be recovered.
3, Reaction liquid extraction: after recovering excessive unreacted formaldehyde and a small amount of by-product methanol, the reaction liquid is added into the organic solvent through the high tank and driven into the extraction column for extraction and separation, and the organic phase containing trimethylolpropane and the by-product dimethylolpropane is collected.
4, Solvent recovery: pump the extracted liquid with organic phase into the solvent recovery column for a concentrated distillation to recover the solvent. The recovered solvent can be returned to the previous extraction process for recycling.
5, Trimethylolpropane distillation: the mother liquor recovered by solvent is then rectification. The trimethylolpropane and the by-product dimethylolpropane can be obtained by controlling the separation of different fractions.
6, Trimethylolpropane preparation: the refined trimethylolpropane product after distillation is directly sent to the production machine for cooling and slicing packaging.
7, Evaporation and concentration of raffinate: the extracted raffinate is pumped from the storage tank into the single-effect evaporator, and forced circulation heating and evaporation are carried out through the circulation pump.
8, Calcium formate separation: the mother liquid containing calcium formate crystallization after concentrated evaporation is driven into the mother liquid high level tank by the circulating pump and into the centrifuge for separation.
9, Calcium formate drying: after separation, the water-bearing calcium formate is sent into the airflow drying tower by the screw propeller and then into the bin through the cyclone separator after drying.
10, Packaging: dried calcium formate products are fed into the meter by a propeller and packaged.
In addition, the following supplementary explanations are also required:
( 1 ) In the process of condensation, in order to reduce the processing capacity of subsequent mother liquid and reduce the cost of alkaline catalyst, it is best to choose high content (95%) calcium hydroxide.
(2)In order to facilitate the refinement of TMP products, the methanol content in the raw materials used for formaldehyde needs to be strictly controlled.
(3) In this project, due to the need to separate the by-product ditrimethylolpropane for sale, it is necessary to further optimize the technological conditions of condensation reaction and control the amount of formaldehyde raw material to be added in the subsequent detailed engineering design. In addition, the process control conditions for separating by-products by distillation should be further optimized.
(4) Because of the low freezing point of trimethylolpropane, the products after rectification need to be cooled by the production machine, sliced and packaged.
2, Trimethylolpropane has broad market potential and good market prospect in China. The implementation of this project can provide high-quality products, meet the market demand, reduce imports, reduce the dependence on foreign products, with good social benefits.
3, The technology is advanced, reliable, equipment manufacturing can be based on domestic.
4, The process has no exhaust emission under normal production conditions; A small amount of waste water can be treated into the circulating water system as supplementary water, and the waste residue can be discharged according to the national standard after treatment.
Main raw material consumption
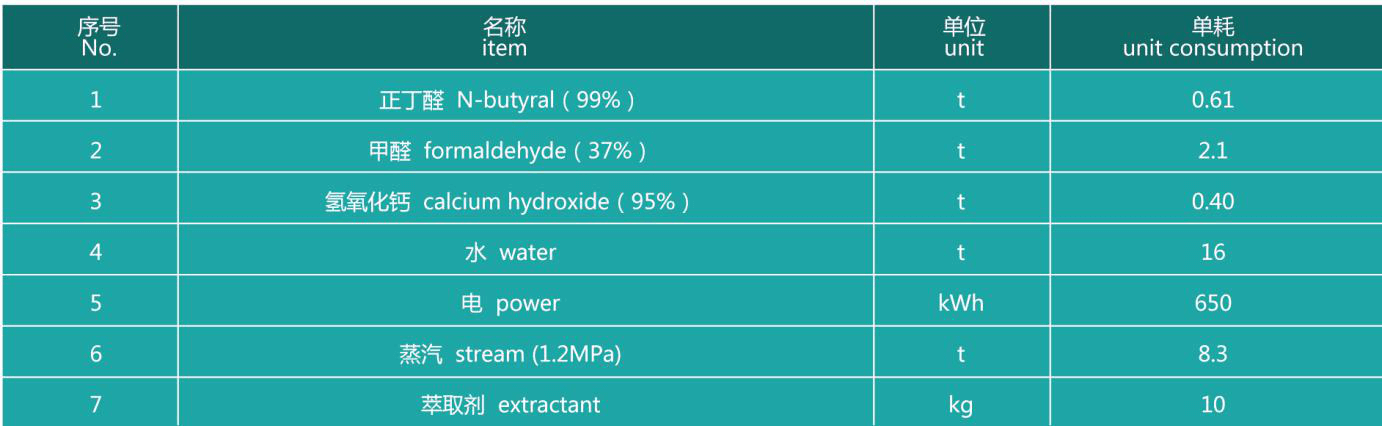
Product Quality
Trimethylolpropane product specifications
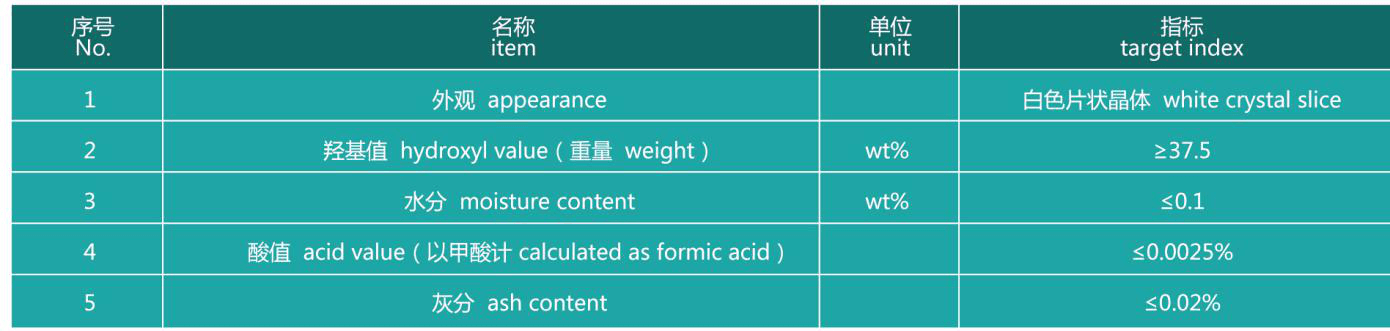
Calcium formate product specifications
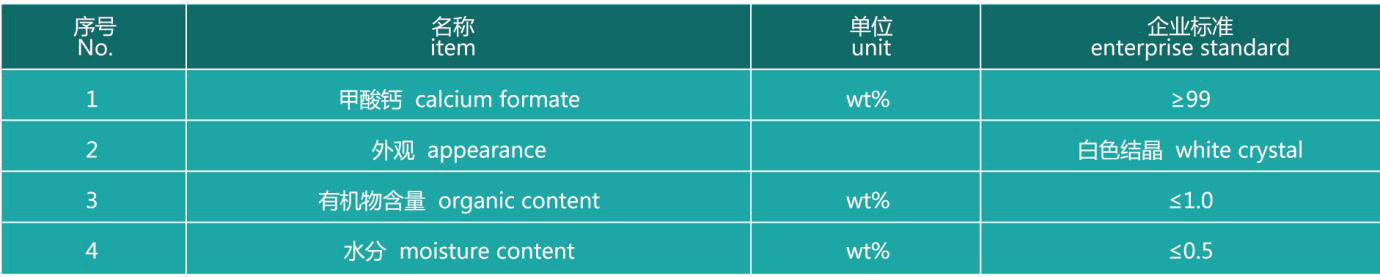
- About Dolton & Helipont
- Formaldehyde production technology
- DMMn production technology
- Paraformaldehyde production technology
- Methylal production technology
- Hexamine production technology
- Acetaldehyde production technology
- Pentaerythritol production technology
- Trimethylolpropane production technology
- Neopentyl glycol production technology
- Trimeraldehyde production technology
- 1, 4-cyclohexane dimethanol CHDM production technology
- EPP production technology
- Production technology of concentrated formaldehyde made from dilute formaldehyde