Introduction of paraformaldehyde properties
Paraformaldehyde has two types: low polymerized paraformaldehyde and solid paraformaldehyde, mainly by the degree of polymerization of formaldehyde - chain number of formaldehyde molecule n, low polymerized paraformaldehyde n < 12, water soluble, fully depolymerized, loose product with uniform particles, is the ideal raw material of pure formaldehyde as well as good substitute industrial formaldehyde, it has great potential in development.
Application of paraformaldehyde
Paraformaldehyde is mainly used in
( 1 ) Farm chemical: synthesis of ethyl oxalamide, butyl oxalamine and glyphosate
( 2 ) Medicine: produce vitamin A
( 3 ) Coating: synthetic high-grade automotive paint
( 4 ) Resin: used in synthetic resin (such as ion exchange resin, melamine resin, etc.), of which 70-80% is used in the production of pesticide synthetic glyphosate herbicide. In the resin industry, paraformaldehyde is used to replace 37% of industrial formaldehyde to produce phenolic resin, which can not only produce high-quality thermoplastic and thermosetting phenolic resin, but also greatly reduce the discharge of waste water and material consumption by more than 10%.
Paraformaldehyde production process
At present, there are two production processes of paraformaldehyde: one is vacuum rake dryer process; the other is spray dryer process.
Rake dryer process
The raw formaldehyde is firstly dehydrated for concentration to increase from 37% to 65%. Then it is sent to the rake dryer for further dehydration and drying until the powder is discharged. The whole dehydration process is operated under negative pressure. The evaporative condensate containing 10-15% dilute formaldehyde returns to formaldehyde section, which is configured as 37% formaldehyde for export or to produce methylal and hexamine. This process is a batch operation, each feed to rake dryer is 4-5m3, drying time is 4-6 hours, the processing cycle is long with low output, and product is powder block.Spray dryer process
Formaldehyde is repeatedly concentrated under the vacuum conditions to increase the concentration up to 85%, and then pumped into spray dryer. Concentrated formaldehyde is ejected from the nozzle and condensed into granular paraformaldehyde solid. This process will produce low polymerized formaldehyde molecules chain with continuous production process, short time concentrated formaldehyde spray granulation and the product has good water-solubility.
Production technology of low polymerized paraformaldehyde
Low polymerized paraformaldehyde is carried out according to the following equation
nCH2(OH)2→(CH2O)n·H2O+(n-1)H2O
In order to obtain paraformaldehyde with low polymerization, the following problems must be noted:
( 1 ) When formaldehyde concentration is processed, dehydration, polymerization and depolymerization are carried out at the same time. If the process condition is not well controlled, it is easy to cause big loss of formaldehyde or block polymerization system.( 2 ) Formaldehyde content is low in the process of concentrated drying, water content is large, and the product is sticky and easy to agglomerate.
( 3 ) Due to the small amount of methanol, formic acid and other polar molecules in the raw formaldehyde, when these substances are concentrated and solidified, they will lead to the continuous polymerization of paraformaldehyde and the formation of insoluble polymers.
Formaldehyde concentration
Formaldehyde solution is a kind of copolymerized mixture: it is mainly composed of methylene glycol CH2(OH)2, polyoxymethenyl alcohol HO(CH2O)nH and hemiacetal HO(CH2O)n-1H. Monomeric formaldehyde is very rare and does not exceed 0.1% (wt) even in concentrated formaldehyde solutions. The water in formaldehyde solution is in two forms: free water and combined water. Combined water is the concentration of water in formaldehyde hydrate molecules, which is related to degree of polymerization and concentration of formaldehyde (refer to the following table).
Relation table of combining water and degree of polymerization ( Unit wt% )

Equipment structure
When designing spray tower, what exerts great influence on product quality will be related to spray pressure, spray angle, spray tower diameter, height, material staying time in the tower, cooling medium temperature, flow rate and so on. For example, concentrated formaldehyde curing temperature closely related to the height of tower; Overheated spray temperature will lead to soft and sticky particles, easy scaling and affecting continuous operation.
Paraformaldehyde flow chart
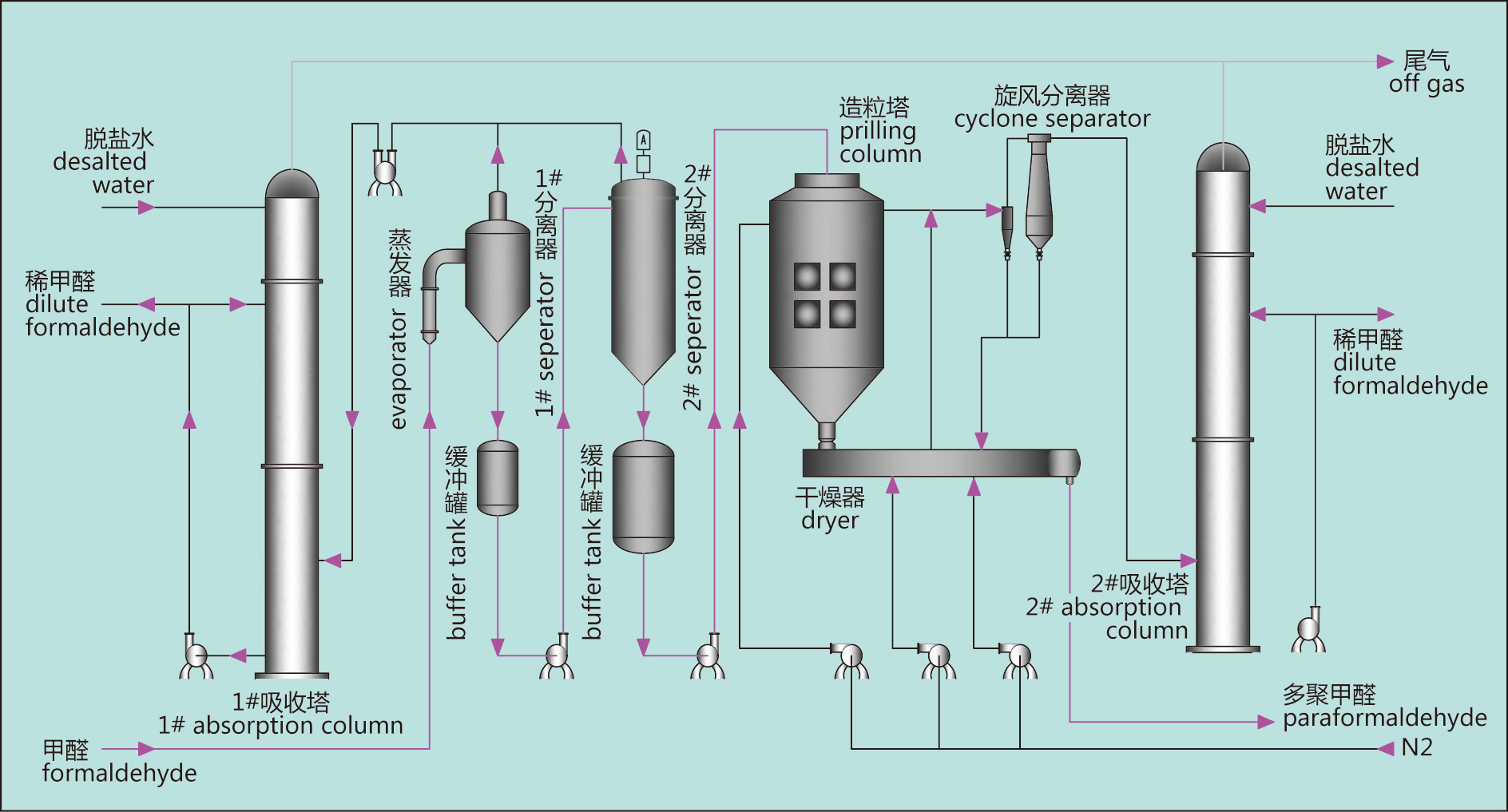
Main consumption index
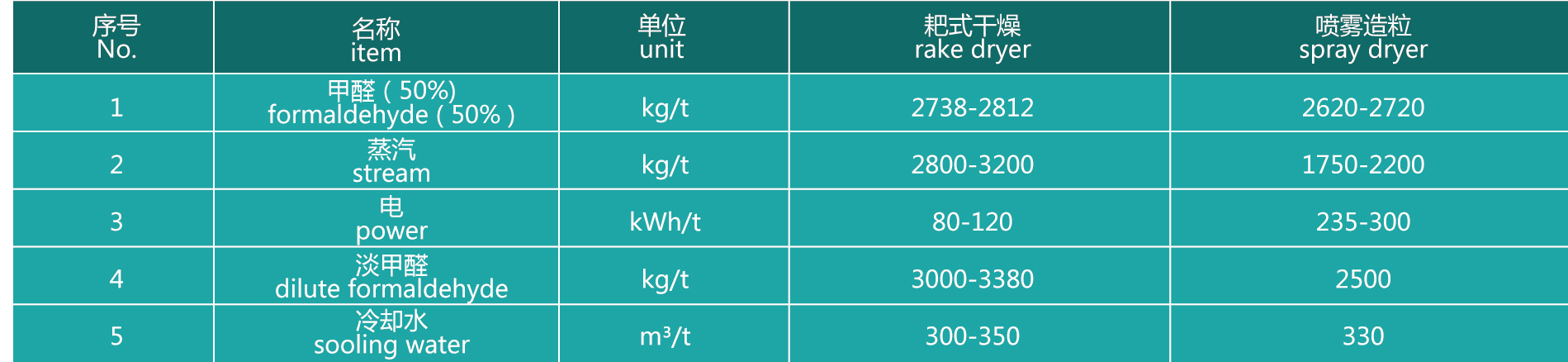
- About Dolton & Helipont
- Formaldehyde production technology
- DMMn production technology
- Paraformaldehyde production technology
- Methylal production technology
- Hexamine production technology
- Acetaldehyde production technology
- Pentaerythritol production technology
- Trimethylolpropane production technology
- Neopentyl glycol production technology
- Trimeraldehyde production technology
- 1, 4-cyclohexane dimethanol CHDM production technology
- EPP production technology
- Production technology of concentrated formaldehyde made from dilute formaldehyde